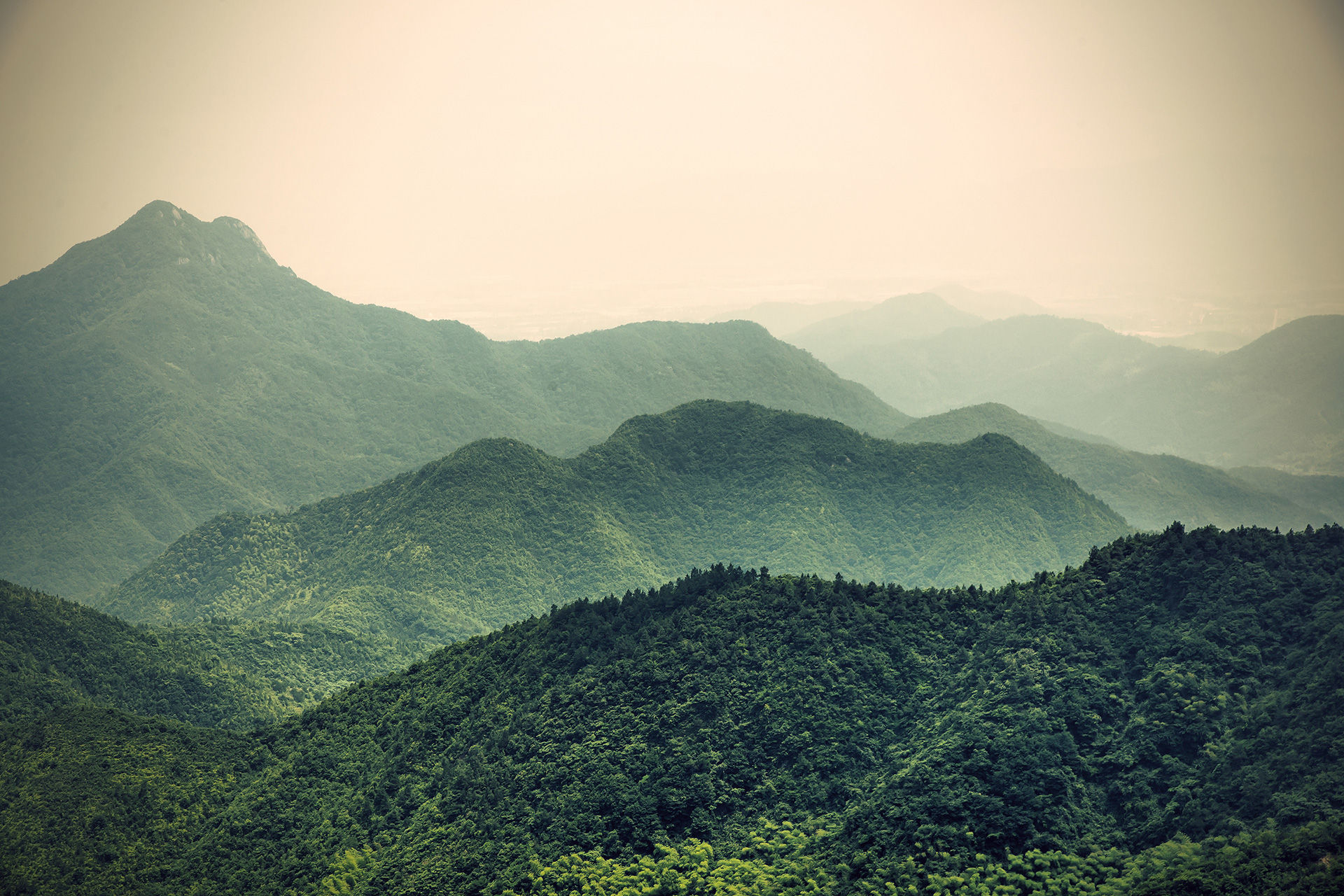

Systems for Hybrid-Additive Process Engineering (SHAPE) Laboratory
December 2017 - May 2019
Skills: SolidWorks, STAR-CCM+, SOLIDCast, 3D Printing, 3D Sand Printing
I joined the SHAPE Lab in December of 2017 to learn more about manufacturing. I have always possessed an interest in knowing how things are made. As a designer, this knowledge helps me understand if a design is feasible, and how to design for manufacturability. I realized the need to understand these concepts during my numerous design projects at Rowan University. My focus with the SHAPE Lab has been on metal casting and 3D sand printing.
Evaluation of 3D Printed Sand Mold Thermal Properties with Variable Binder Ratio:
Paper: Towards Functionally Graded Sand Molds for Metal Casting: Engineering Thermo-mechanical Properties Using 3D Sand Printing
Martinez, D., Bate, C. & Manogharan, G. Towards Functionally Graded Sand Molds for Metal Casting: Engineering Thermo-mechanical Properties Using 3D Sand Printing. JOM 72, 1340–1354 (2020). https://doi.org/10.1007/s11837-019-03975-x
Successful castings are often the result of accurate solidification simulation. Simulations can only be successful if property inputs accurately reflect real-world values. Numerous studies have been conducted to quantify the values density, thermal conductivity, and specific heat in traditional green sand mold; however, these values remain unknown for 3D printed sand molds. The growing popularity of these innovative molds made it imperative to quantify these values for the casting industry. Property measurements were taken using traditional material testing devices and compared to the results of a cooling curve experiment. Variable binder to sand ratio serve as an additional point of study. The effects of changing this ratio had been categorized for mold strength; however, thermal properties had not been explored.
Experimental Metal Casting Hydrodynamics and Proposal of Succinonitrile Analog:
Due to the harsh environments under which metal casting takes place, experimental analysis of metal casting has taken a back seat to numerical computer models. With the increase of computing ability in the 1990's, the decade and early parts of the new millennium were dominated by numerical simulation models. Sensors are generally incapable of surviving casting conditions so experimental analysis has been largely reserves to qualitative video analysis. This is very expensive, however, because an x-ray device must be used to see through the opaque sand walls. Given these challenges, the most common form of experimental casting analysis in to use water to simulate the mold filling. While water and liquid metals are different in many ways, this is the manner in which many numerical models have been derived and/or validated.
Succinonitrile (SCN) is a clear plastic crystal that melts at relatively low temperatures. Because it forms dendrites when it solidifies, SCN has a long history as a metal analog in solidification research. My work with the SHAPE Lab proposed that SCN is as good or better than water as a metal analog and therefore should be considered as a resource to conduct experimental casting hydrodynamics research. My work used commercial CFD tools to simulate aluminum, water, and SCN filling the sand casting geometry. I have also conducted a series of experimental tests using SCN and acrylic molds of the same geometry. High speed video was taken of the acrylic mold filling. This video is being compared to a x-ray images in 1995 study of aluminum filling a sand mold of the same casting geometries. This work hopes to propose SCN as an experimental method for better understanding the physics of casting hydrodynamics.
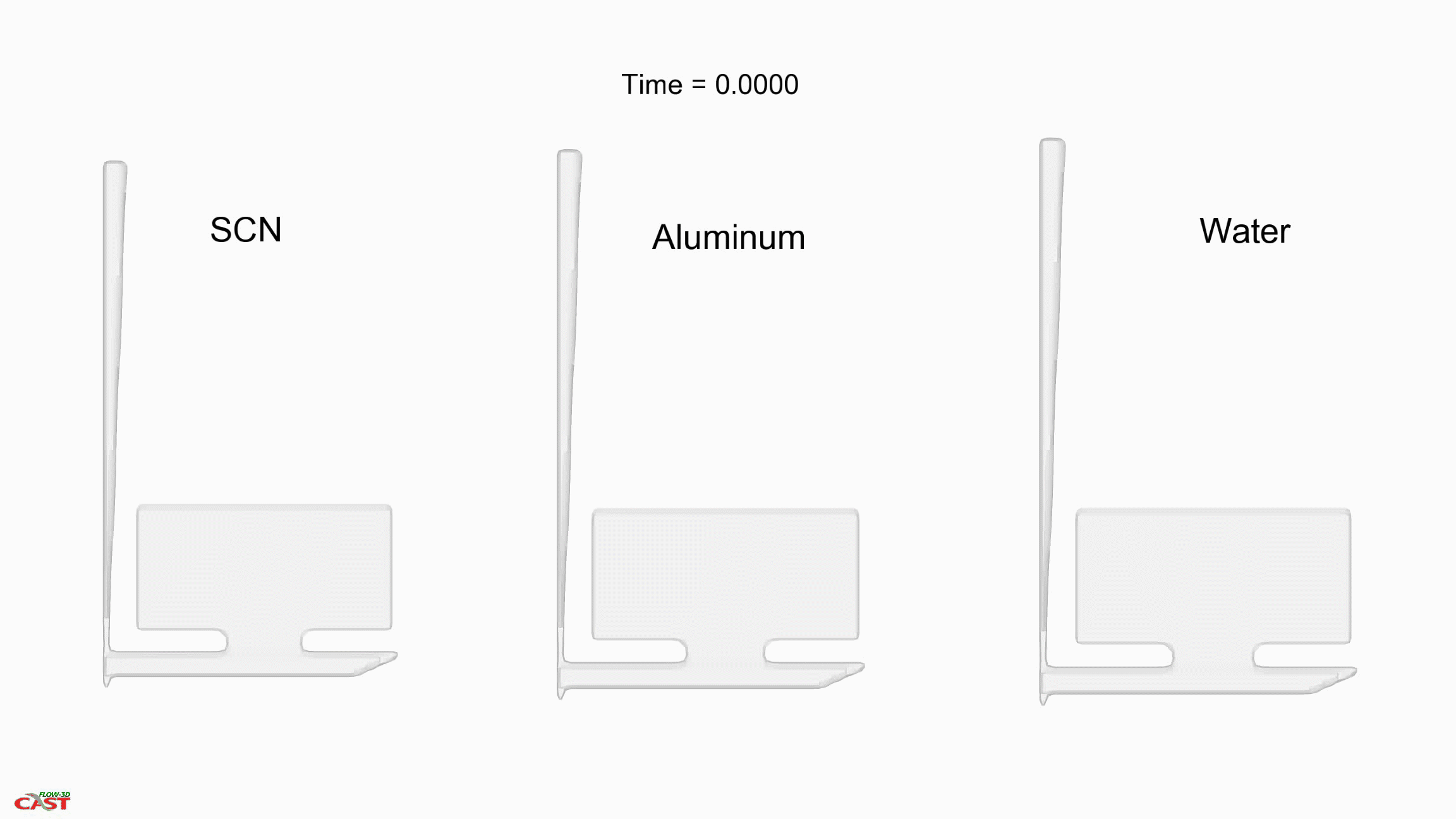
3D Sand Printing Hub Location Study
This study is being headed by our friends at North Carolina State University. This goal of this paper is to use a regression model to determine the optimal location for 3D sand printing (3DSP) hubs to be placed around the U.S. 3DSP is optimally suited for low production, high complexity parts. This niche leaves it too small for many large manufactures and too costly for many small manufacturers. Therefore, a network of 3DSP hubs may over the best cost and availability solution to the need for 3DSP.
My contributions to this study included identifying a group of commonly used parts that are best suited for 3DSP manufacturing. I developed the CAD for these potential sand molds and gathered printing quotes from current 3DSP vendors. The quotes acquired were used in the regression model. Additionally, I conducted I conducted a literary review of 3DSP development and its roles in the casting market.