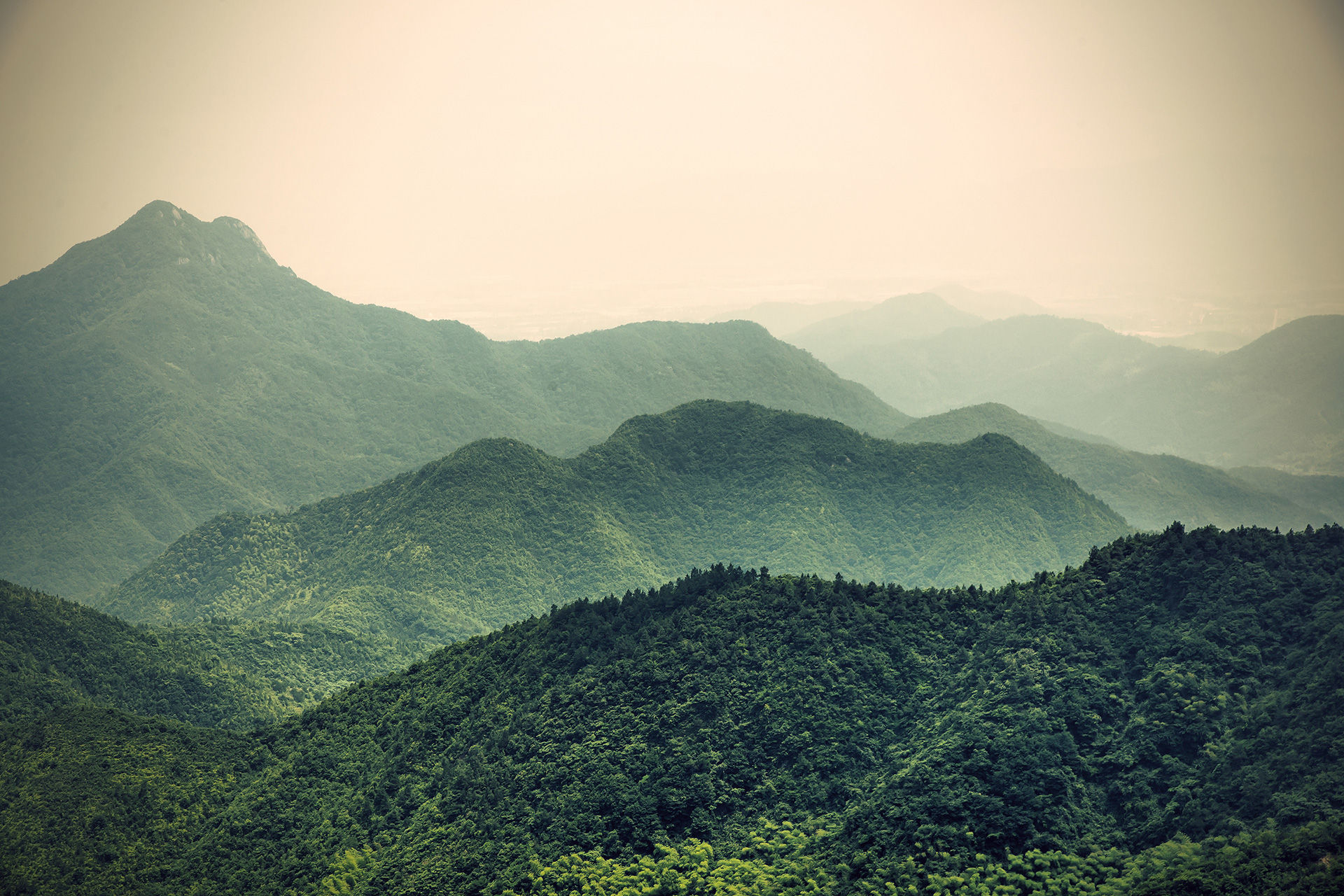
Underwater ROV
Sophomore Engineering Clinic II, Sophomore Undergrad
Team members: Christopher Boyle, James Scroth, Carmine Adames
Skills: Solidworks, Lasercutting, Waterjetting, PVC Assembly


Testing Goals
-
Straight line speed
-
Obstacle course speed
-
Object pick-up
Keys to success
-
Align center of mass and center of buoyancy in X and Y axis
-
Maximize distance between COM and COB in Z axis
-
Keep COM and COB at center of ROV in XZ and XY planes

_JPG.jpg)


Given supplies:
- 1 motor control box - 3 electric motors - unlimited pool noodles
The Frame
-
Simple PVC rectangular prism
-
Keep small in overall scale
Mounting Components
-
Central acrylic plate for control box and motor
-
Maximize porosity to minimize forces on plate during turns
-
Aluminum brackets for motor mounts
COB vs COM
-
Open access to bottom PVC links allowing for hollow spaces to be filled with ballast material
-
Cover top members with pool noodle
-
Designed using Solidworks sheet metal functions
-
Maximize porosity to reduce drag
-
Water jetted as flat piece
-
Bent to design specs
The Scoop
Build changes:
During the build, a decision was made to cut holes into the PVC frame. These holes allowed water to fill the entire frame taking up space that would normally be filled with air and sealed off. This eliminated the un-modeled buoyant air inside the frame resulting in the pool float being the dominate buoyant member.